PENN NATIONAL RACETRACK
JULY, 2008
After securing a Pennsylvania state gaming license, Penn National Gaming Inc. of Wyomissing, PA determined their next step was to build a Hollywood-themed casino with racetrack and slot parlor on the site of the existing Penn National race track facility. To pave the way for a new grandstand and slot parlor, Carlino Development and Reynolds Construction secured the services of NADC, member Empire Wrecking Co. of Reading, PA (Empire) to handle the enormous task of the demolition of the existing facilities. The primary objective of Empire was to demolish the 34-year-old racetrack grandstand located on Route 743 in Grantville, PA.
Accordingly, Empire began the project with the removal of several individual buildings to allow for the construction of new support buildings and equine stalls. As demo of this initial phase approached completion, Empire swiftly began phase two of the demolition of the historic Penn National half-mile dirt stock car track’s interior and exterior concrete perimeter. Empire tackled the stock car track’s concrete wall with a John Deere 450 grapple machine and a 330 with a digging bucket. In this phase, Empire hauled away 365 loads of concrete to its dump site. Some of the pieces of the concrete walls were over 28 feet long and weighed in excess of 20 tons, necessitating the need for a specialty trailer to haul the massive pieces of concrete. In conjunction with the demolition and removal of the concrete walls, Empire’s professional team utilized a John Deere 330 to rip down the grandstand and John Deere 270 machine to hammer and remove concrete. When the “dust had settled,” Empire had hauled 15 loads of scrap metal, 365 loads of concrete and 27 loads of debris. The entire process of tearing down the stock car track and grandstands took approximately three weeks and was completed on time and within budget. This area will be used for future expansion.
Upon completion of the first two phases of the project and immediately upon notice to proceed, Empire commenced with the demolition of the main grandstand building. This structure consisted of four stories equaling 300,000 sq. ft. and was used for viewing daily horse racing, simulcast wagering, and administrative offices.
Empire was afforded just sixty days to complete the project or risk a hefty $10,000 a day liquidation penalty. With the purpose of meeting the critical deadline, Empire mobilized their Hitachi 450 with the 95-ft. boom and their newl-acquired John Deere 450DLC, also with a 95-ft. long boom. John Deere, Plasterer Equipment, and Lemac worked closely with Empire to have the machine delivered to the site and set up in time for the groundbreaking. The John Deere 450DLC was one of the first to hit the market and the boom was actually sent to Lemac for modification prior to this machine being released for shipment. This modification was exactly what was needed for the start of the job and to make it possible to meet the deadline. The combination of the two machines made quick work of this concrete and steel monster. As demo of the grandstand building continued, Empire also mobilized several loaders along with John Deere excavators ranging in size from 200 to 350 series to separate and load the enormous amounts of debris, steel, and concrete further enabling Empire to keep the project on schedule.
In the process of tearing down this famous facility, many different attachments were added to the equipment utilized on the project. At any given time, there were two Labounty shears in operation to cut the steel to a length that would fit into the numerous trailers used to haul the scrap and debris to facilities. In addition, Empire had concrete processors on site to crunch the concrete to proper size to be hauled away in the tri-axles and trailers.
Moreover, the project was staffed with one superintendent, two working foremen, and ten full-time laborers. Empire had numerous laborers picking through the processed concrete to remove all steel and debris to make the material suitable to be used as clean fill on another project. There were nine operating engineers assigned to handle the variety of equipment in use and fifteen trucks on-site to move the massive piles of scrap and debris. As the targeted completion date neared, Empire was able to downsize its crew of professionals. At the end of the project, it was determined that Empire had moved 3,000 tons of debris along with 1900 loads of concrete and dirt, as well as 2500 tons of steel from the grandstand area.
The Empire crew worked five ten-hour days and eight hours on Saturday. Work hours on the main grandstand had to be curtailed from 7 am to 9 am in order to allow the horses on the track for their morning workouts (any loud noises or amount of dust could potentially spook the thoroughbred horses). Empire utilized the time to focus on the front side of the building, thus ensuring that there were no problems or interruptions to the horses’ daily schedule.
Despite the sizable project, the aggressive timeline, and logistical restrictions, Empire’s highly-qualified team rose to the challenge, as always, and handled the project with expertise and professionalism. Completing jobs of this size on budget and on time is only possible by having good people within your company that stand up to the challenge and handle it. From the estimators, operations managers, operators, dispatcher, superintendent, foremen, truck drivers, and laborers - all performed admirably. This is proof that it takes a true team effort.
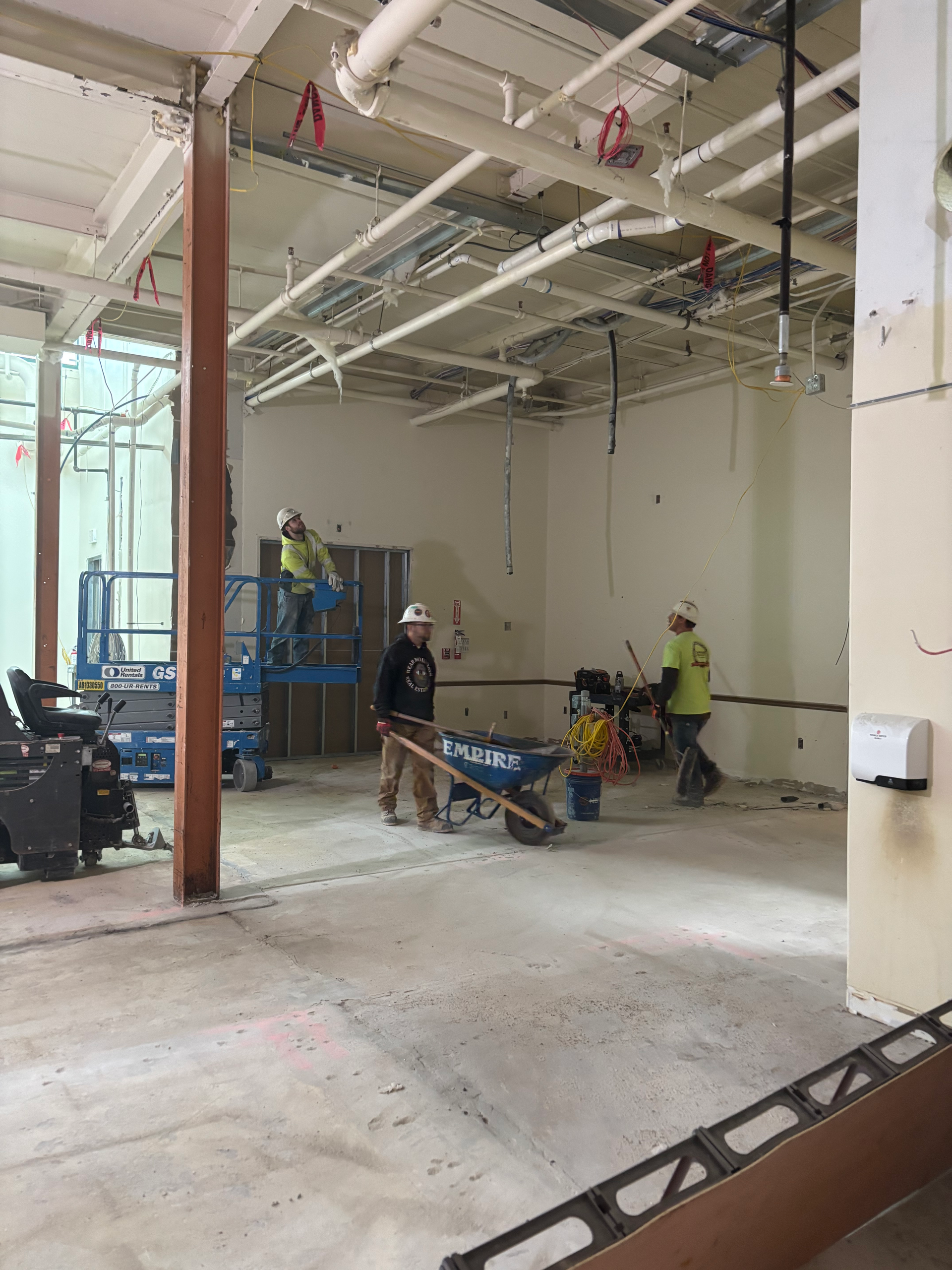
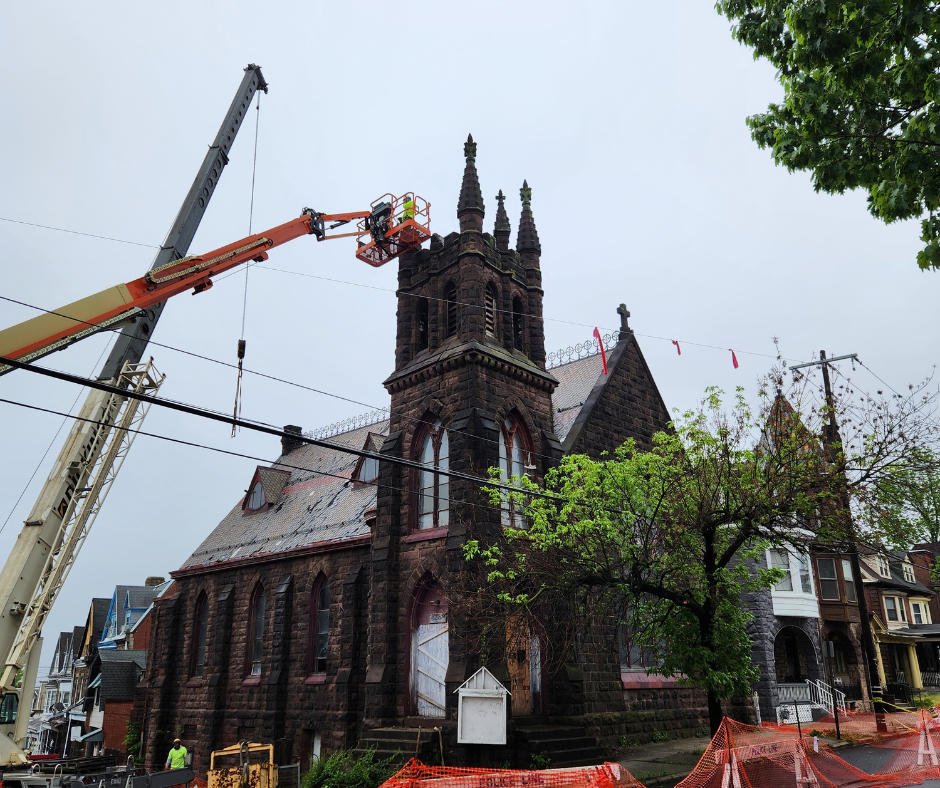
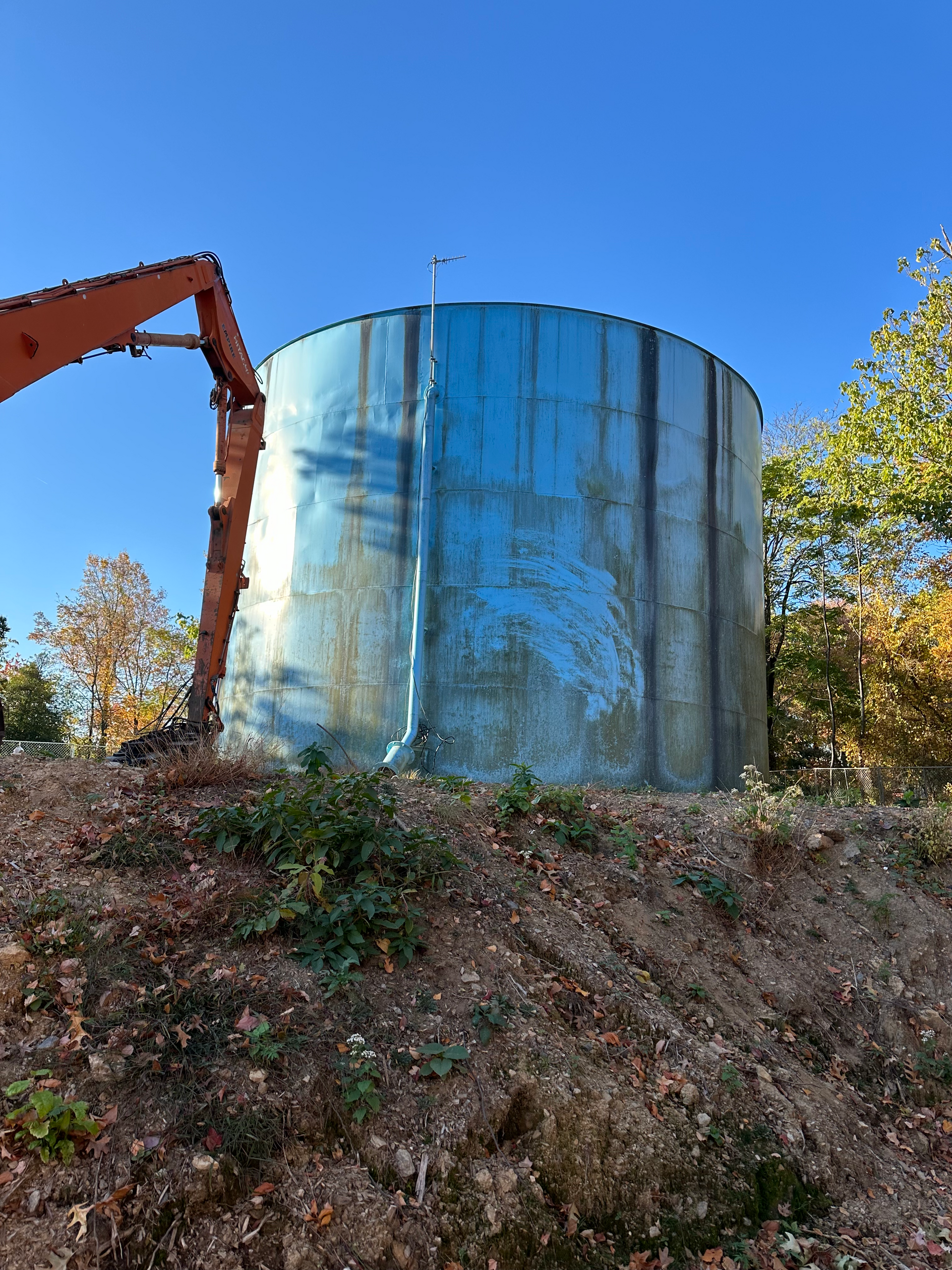
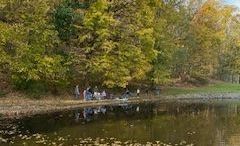
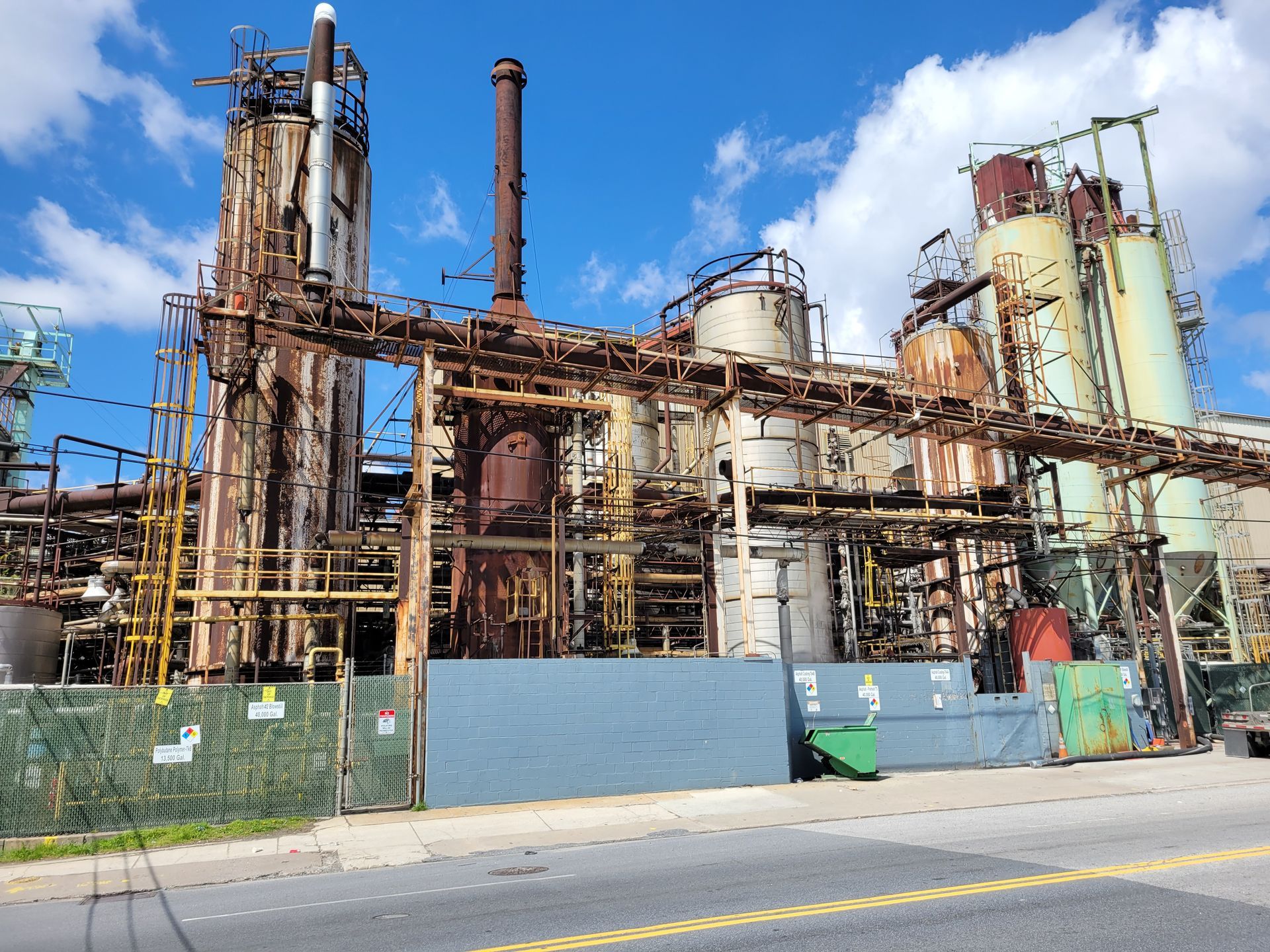