Precision Dismantling: Navigating Challenges in the Heart of Manufacturing
In the ever-changing world of manufacturing, the integration of automated systems is often crucial to enhancing efficiency and streamlining production processes. However, when the time comes to upgrade or replace these systems, the challenges of dismantling them without disrupting daily operations can be both complex and demanding. In a recent project, Empire Services undertook the task of dismantling a local truck body manufacturer's current automated system.
Empire Services took on the responsibility of dismantling portions of the current automated lifting system, which is deeply embedded within the manufacturer's facility. This automated system, serving as the backbone of their manufacturing process, needed to operate seamlessly every day. To navigate this challenge, the project was divided into four phases, with the crucial stipulation that the system could only be removed during facility shutdowns to avoid disruptions to daily operations. The entire project is expected to be completed this fall.
The Intricacies of the Automated System
The complexity of the automated system lay not only in its integral role in the manufacturing process but also in its extensive structural integrity. The system, responsible for lifting and transporting truck bodies from station to station and situated on a multi-level mezzanine that winds its way throughout the facility, required a strategic dismantling approach.
To execute the dismantling, the Empire Services team employed a combination of tools and equipment, including aerial lifts and various forklifts. The primary tool for the task was an acetylene torch, skillfully wielded to cut the steel structures into manageable pieces. The precision required in this process was heightened by the challenges posed by the confined space and the need to navigate around existing production equipment that could not be easily relocated.
Navigating Space Constraints
One of the primary hurdles faced by the team was the limited operating space. The structures earmarked for removal were situated in the heart of the manufacturing floor, surrounded by various production equipment that couldn't be moved. This necessitated a careful maneuver around, on top of, and beside the operational machinery, emphasizing the team's adaptability and precision in their approach.
Working with steel structures at significant heights added an additional layer of complexity to the project. Cutting and lowering steel components required heightened safety measures, and the team's expertise ensured a meticulous and smooth process. The use of aerial lifts allowed for controlled access to elevated sections while forklifts ensured safe handling of these materials, showcasing the team's commitment to both efficiency and safety.
The dismantling of an automated system within a manufacturing facility is no small feat, and the success of Empire Services in navigating the complexities of this project stands as a testament to our expertise. From strategic planning and phased implementation to adapting to space constraints and ensuring safety at every step, the precision dismantling of this automated system exemplifies the delicate balance required in such endeavors. As manufacturing technologies continue to evolve, the ability to efficiently upgrade or replace systems while minimizing disruptions remains a crucial skill, and Empire Services has showcased its expertise in executing this intricate balance of precision dismantling.
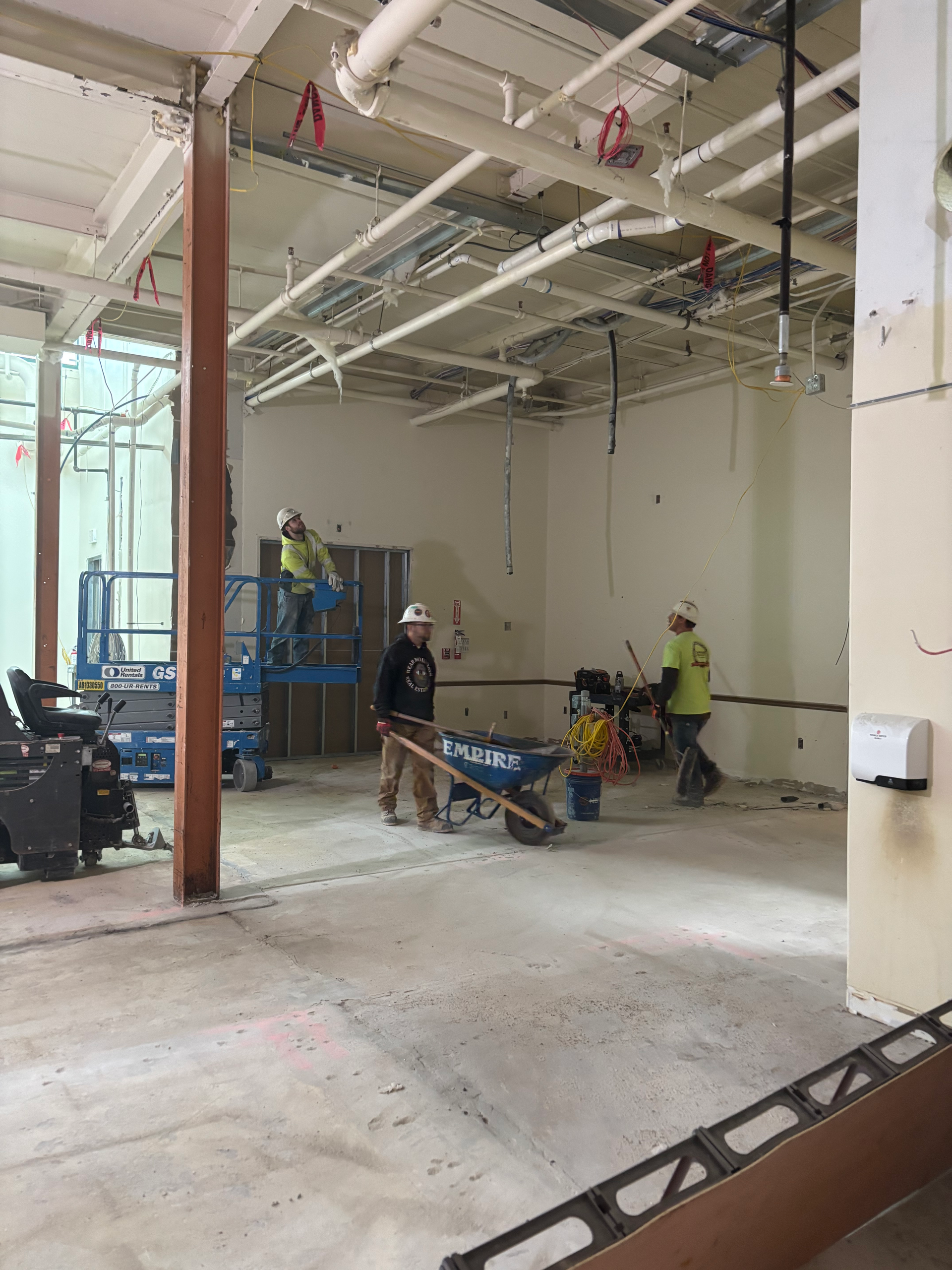
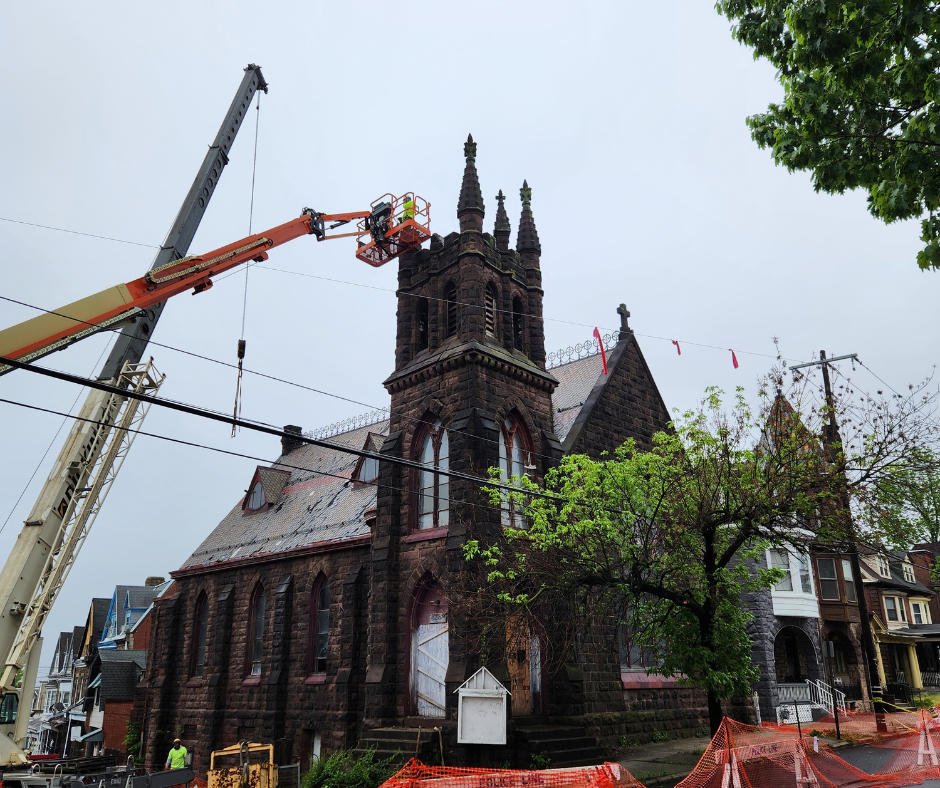